In the realm of automotive maintenance and repair, understanding the process of servicing different components is crucial. One such component that often needs attention is the brake rotor, also known as the brake disc. This component, which the brake pads clamp down on to stop your vehicle, can wear down or become damaged over time. Consequently, there will be instances where you’ll need to remove the brake rotor for servicing or replacement.
How to Get a Brake Rotor Off – it’s important to note that while the procedure might appear straightforward, it sometimes poses a challenge due to rust, wear, and the accumulation of brake dust. A variety of tools and techniques can come into play, from simple hand tools to penetrating oils. It’s also essential to understand how to do this safely to avoid damage to the vehicle or potential personal injury. In this article, we’ll walk you through a comprehensive, step-by-step guide on how to get a brake rotor off, equipping you with practical knowledge for your DIY automotive maintenance tasks.
Contents
- 1 Key takeaway:
- 2 Introduction to the issue of a stuck brake rotor and its potential consequences
- 3 Steps to remove a stuck rotor
- 4 Importance of replacing rusted components like brake pads and shoes
- 5 Specialized tools and precautions to consider for the job
- 6 If the rotor remains stuck, alternative methods to try
- 7 Preventive measures to avoid future stuck rotors
- 8 Conclusion highlighting the importance of seeking professional help if unable to dislodge the rotor and the significance of preventive maintenance measures
- 9 Some Facts About How To Get Brake Rotor Off:
- 10 FAQs about How To Get Brake Rotor Off
- 10.1 How do I remove a stuck brake rotor?
- 10.2 What are some tips to prevent a stuck rotor in the future?
- 10.3 Do I need to be a professional mechanic to remove a stuck rotor?
- 10.4 What should I do if the rotor is still stuck after following the steps?
- 10.5 Should I seek professional assistance if I’m unable to remove the stuck rotor?
- 10.6 How can I safely remove a stuck brake rotor without damaging other components?
Key takeaway:
- Addressing rust and corrosion on brake components is crucial to prevent a stuck brake rotor and its potential consequences.
- Steps to remove a stuck rotor include removing the brake caliper from the bracket, removing the caliper plate, temporarily reattaching the lug nuts, removing rust from the rotor, and using specialized equipment for the process.
- If the rotor remains stuck, alternative methods to try include rotating the rotor, using penetrative lubricant, utilizing a rotor puller, applying heat, using a breaker bar for leverage, and cutting the rotor off with an angle grinder as a last resort.
- Preventive measures to avoid future stuck rotors include cleaning rust and corrosion, and applying grease or lubricant to the wheel hub and rotor surface.
- Seek professional help if unable to dislodge the rotor and prioritize preventive maintenance measures to ensure the safety and functionality of the braking system.
Introduction to the issue of a stuck brake rotor and its potential consequences
Rust and corrosion on brake components can lead to a common issue – a stuck brake rotor. This Introduction explores the consequences of this problem and highlights the importance of addressing rust and corrosion to ensure smooth and safe braking.
Importance of addressing rust and corrosion on brake components
Addressing rust and corrosion on brake components is vital for the safety and function of the braking system. Rust can get stuck or corroded on rotors, calipers, and other parts, reducing braking performance, increasing stopping distances, and possibly causing brake failure.
To remove a stuck rotor, it is essential to follow specific steps:
- Take off the brake caliper from the bracket.
- Take off the caliper plate for further clearance. Temporarily reattach the lug nuts to stabilize the rotor during removal. To get rid of rust, use penetrating lubricant, bolts in the back of the rotor, or a rotor puller.
Replacing rusted brake pads or shoes is necessary for optimal braking performance. Rusted pads may not grip the rotor surface, reducing stopping power. Rusted shoes may also not engage properly with drum brakes, affecting their performance.
When dealing with a stuck rotor, use a breaker bar for leverage and caution when using heat. If alternative methods do not work, seek professional help. It is important to take preventive measures against future stuck rotors by regularly cleaning rust and corrosion and applying grease or lubricant.
Pro Tip: Regularly inspect brake components for rust and corrosion to spot potential issues and prevent more severe issues.
Steps to remove a stuck rotor
In this section, we will explore the steps to remove a stuck rotor, including removing the brake caliper from the bracket, removing the caliper plate, temporarily reattaching the lug nuts, removing rust from the rotor, and using additional equipment for the process. We’ll also discuss the technique of inserting bolts into threaded holes at the back of the rotor. These steps will provide you with a comprehensive guide to successfully removing a stuck brake rotor.
Remove the brake caliper from the bracket
To sort the issue of a stuck brake rotor, it is imperative to take out the brake caliper from its bracket. Take care to do this carefully and effectively.
This can be achieved by carrying out the following four steps:
- Locate and loosen the bolts that attach the caliper to the bracket.
- Slide off the caliper from the bracket. Beware not to damage or stretch any brake lines connected to it.
- Put the caliper aside in a secure place, making sure not to hang it by the brake hose.
- Check the caliper and bracket for any wear or damage that might need servicing or replacement.
By executing these steps, you can remove the brake caliper from its bracket securely and proceed with the further maintenance of the stuck brake rotor.
Note that there may be slight differences in bolt sizes or attachment methods depending on the vehicle model. So, consulting a service guide for your vehicle or consulting a professional for guidance may be helpful.
Remove the caliper plate
Removing the caliper plate is essential to dislodge a stuck brake rotor. Access and remove the rotor easily by following these steps:
- Loosen and remove the bolts securing the brake caliper to its bracket.
- Slide the caliper off the bracket, being careful not to strain the brake hose.
- Remove any screws or clips securing the caliper plate to the rotor.
- Pry off the caliper plate with a flat-head screwdriver or pry bar.
- Clear away all grease and debris from both sides of the caliper plate.
By removing the caliper plate, you’ll be able to address any rust or corrosion that may be present on the rotor. Plus, you can inspect and replace brake pads or shoes if needed.
To work efficiently, have wire brushes and sandpaper to clean the rotor’s surface. This ensures optimal contact between the rotor and brake pads.
You can also insert bolts into threaded holes at the back of the rotor to provide leverage for removal. Turn the bolts in a diagonal pattern with a wrench to help loosen any rust.
If you can’t remove the rotor, try rotating it manually, using penetrative lubricant, utilizing a rotor puller tool, applying heat with a torch, using a breaker bar, or as a last resort, cutting it off with an angle grinder.
Prevent future instances of stuck rotors with regular cleaning, applying grease or lubricant, and preventive maintenance. If you still can’t dislodge the rotor, seek professional help. They have the necessary expertise and tools.
Temporarily reattach the lug nuts
Temporarily reattaching the lug nuts is an important step when removing a stuck brake rotor. It helps keep everything stable and prevents any extra movements. Here’s a five-step guide to do it:
- Take the brake caliper off its bracket and put it in a safe place.
- Remove the caliper plate, and don’t forget the bolts and clips.
- Put the lug nuts on the wheel studs.
- Thread each lug nut onto its wheel stud by hand. Make sure they’re tight enough to keep the rotor in place.
- Check that each lug nut is securely tightened with the right tools, like a torque wrench.
This step is only temporary, but it’s essential for control and stability during the removal. Remember to wear protective gear like gloves and eye protection. Taking these precautions will help you complete the task safely and successfully.
Now, here’s a story related to this:
I had a customer who was trying to remove a rusty brake rotor on his own. He followed all the steps, including temporarily reattaching the lug nuts. He managed to remove the rust properly with the right tools and techniques.
He took his time and used the necessary safety precautions. This taught him the importance of regular maintenance and preventive measures. It also showed him when he should seek professional help if he doesn’t have the right tools or expertise.
Remove rust from the rotor
Rust on the rotor is a common issue that can reduce the performance of the braking system. It’s key to take this rust off to have perfect braking and hinder any potential risks. Here’s how to do it:
- Detach the brake caliper from the bracket: Begin by undoing and taking away the bolts that hold the caliper in place. After removing, put the caliper aside with no pressure on the brake hose.
- Take out the caliper plate: After detaching the caliper, find and get rid of the caliper plate or bracket that holds the pads in position. This will give better access to the rotor for cleaning.
- Temporarily attach the lug nuts: Loosely screw a few lug nuts onto the wheel studs. This will stop the rotor from moving while you remove rust.
- Eliminate rust from the rotor: Use sandpaper or a wire brush to scrub any rust from both sides of the rotor. Pay attention to areas where rust can be more evident, like close to the edges or vented areas of the rotor.
- Extra tools needed for the process: If there are strong rust spots that cannot be taken off with sandpaper or a wire brush, consider using particular tools like a rotary tool with a wire wheel attachment or a rust removal solution okayed for use on rotors.
After following these steps, your rotor should be rust-free and ready to use. But if there’s severe corrosion or pitting on the rotor, it may need to be changed to guarantee secure braking.
By taking away rust from your rotors properly, you can upgrade braking performance and stretch their life. Examining and looking after your brakes regularly can aid you to discover any signs of corrosion early, so you can deal with it before it gets worse.
Time to fill up your toolbox, because getting rid of a stuck rotor needs more than just a hammer and a positive attitude.
Additional equipment needed for the process
To remove a stuck rotor, certain items are key. Wrenches or sockets of the correct size for the bolts that hold the caliper in place are needed. A rubber mallet or dead blow hammer is also necessary to tap the rotor and break free any rust or corrosion. To aid in rust removal, use wire brushes, sandpaper, and WD-40.
Manufacturer’s instructions should be followed if any additional tools are necessary, such as retaining clips, caliper piston compressors or specialized brake tools.
One time, a technician faced difficulty in removing a stuck rotor due to rust. Standard wrenches and a rubber mallet failed, so they used wire brushes, sandpaper, and WD-40 instead. Having the right equipment helps greatly when it comes to tackling brake rotor issues.
Like Frankenstein’s book, bolts are inserted into threaded holes at the back of the rotor to bring new life. Extra equipment is essential for a successful procedure.
Inserting bolts into threaded holes at the back of the rotor
When dealing with a stuck brake rotor, one way to address the issue is to insert bolts into threaded holes at the back of the rotor. To do this, you’ll need specialized equipment. Here are the steps:
- Remove the brake caliper from the bracket. This can usually be done by taking off the retaining bolts/pins.
- Take off the caliper plate to expose the backside of the rotor. This might take extra tools depending on your vehicle model.
- Put a few lug nuts back on the wheel studs for security.
- Inspect and clean any rust or corrosion on both sides of the rotor surface using the correct tools.
- If your rotor is stuck, you may need a rubber mallet or pry bar for leverage.
- Look for threaded holes at the circumference of the rotor. Insert bolts into these holes and tighten them.
Remember: Rusty brakes are like a bad relationship – it’s time to break up and find something new!
Importance of replacing rusted components like brake pads and shoes
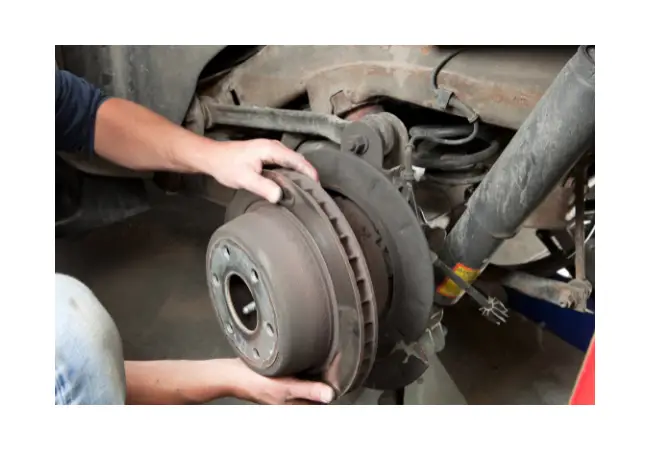
Rusted brake pads and shoes are key for good braking. It’s important to replace them to keep performance and safety optimal. Rust can weaken components, causing longer stopping distances and the risk of accidents.
The grip on the rotor or drum weakens when these components rust. This reduces braking power and can cause uneven wear. Replacing them brings back friction and avoids further damage.
Inspection and maintenance are a must to spot early signs of rust. Moisture and environmental factors can make it worse. Keeping the brake system clean and dry can help, as can using high-quality components that resist rust.
Specialized tools and precautions to consider for the job
John, a car owner, faced the task of removing his vehicle’s brake rotor. Necessary safety precautions and specialized tools were taken. Safety glasses were worn to protect from any flying debris or metal flakes. Jack stands were used to secure the vehicle and provide a stable working environment. A lug wrench was used to loosen and remove the wheel’s lug nuts. A C-clamp compressed the brake caliper piston back into its cylinder. To attach the wheel and keep it safe, a torque wrench was used to tighten the lug nuts with the right torque.
These tools, along with safety gear and vehicle support, are essential for successful brake rotor removal. It’s best to read the vehicle’s manual or get professional help. Lastly, it’s important to handle brake parts with care and cleanliness for their effectiveness and longevity.
John faced challenges due to rusted bolts but still managed to remove and replace the brake rotor. This shows how important it is to use the correct tools and take necessary precautions for easier and safer brake rotor removal.
If the rotor remains stuck, alternative methods to try
When the brake rotor refuses to budge, there are several alternative methods worth considering. From rotating the rotor to applying heat, using penetrative lubricant to utilizing a rotor puller, and even resorting to cutting it off as a last resort with an angle grinder. In this section, we’ll explore these alternative techniques to help you get that stubborn rotor off.
Rotating the rotor
Text: Turning the Rotor:
- Begin by slackening the lug nuts on the wheel with a lug wrench or breaker bar.
- Raise and secure the vehicle using a hydraulic jack and jack stands for safety.
- Remove the lug nuts fully and take off the wheel carefully.
- Reach the brake rotor by removing the caliper assembly and brake pads as explained in earlier steps.
- With the caliper assembly away, try to rotate the rotor using your hands or a rubber mallet if needed.
- Utilize steady pressure while attempting to rotate, being careful not to apply too much force that could damage the rotor.
If rotating the rotor doesn’t work, there are alternative approaches to try, such as using penetrative lubricant, using a rotor puller, applying heat, or using a breaker bar for added leverage. However, it is essential to be mindful and think about seeking professional help if unable to detach the stuck rotor. Preventive measures mentioned earlier, such as cleaning rust and corrosion and applying grease or lubricant to avert future sticking issues, should also be taken into account for ongoing maintenance.
Using penetrative lubricant
Text:
Penetrative lubricant is great for freeing stuck brake rotors. It seeps into small places, dissolves rust, and reduces friction. This helps remove the rotor without damaging it or using too much force. It also prevents future rust and corrosion. For optimal performance, choose a high-quality penetrative lubricant made for automotive use.
If the rotor still won’t budge, try other methods. Rotate it, use a rotor puller, apply heat, lever with a breaker bar, or cut it with an angle grinder as a last resort. But be careful – these methods come with risks.
Utilizing a rotor puller
A rotor puller is a handy tool for taking off stuck brake rotors from vehicles. It is an invaluable tool that helps in removing the rotor when other methods have failed. A rotor puller applies pressure to separate the rotor from the wheel hub safely and efficiently.
To use a rotor puller:
- Make sure the car is on jack stands or a lift.
- Take off the brake caliper and bracket from the rotor. This will give access to it.
- Attach the rotor puller by inserting its hooks into the appropriate positions.
- Fasten any adjustment screws or nuts on the puller to make sure it’s secure and in the right place.
- Apply gradual pressure with hand tools or hydraulics until the rotor comes away from the wheel hub.
- If needed, keep tightening or adjusting it until it is fully free.
Be cautious when using a rotor puller, as it can damage wheel bearings or wheel studs. Make sure it is aligned and positioned correctly.
Also, using a rotor puller should only be done after other methods have been tried. If you struggle, get professional help.
A mechanic once wanted to remove a brake rotor with different methods without success. As a last resort, he used a rotor puller. With the right pressure and positioning, he got the rotor off without damaging anything. This proves how useful a rotor puller can be when other techniques are exhausted.
Applying heat
To safely apply heat to a stuck rotor, follow these steps:
- Wear protective gloves and eyewear.
- Use a heat source like a propane torch to evenly heat the rotor.
- Avoid prolonged exposure in one area to avoid warping.
- Periodically rotate or tap the rotor lightly with a rubber mallet to help loosen it.
- After heating for a while, carefully try to remove the rotor with a rubber mallet.
- If the rotor does not move with heat and other techniques, get professional help.
It’s important to use heat with caution and only if other methods are ineffective. Excessive force or incorrect use of heat can cause more damage.
Prevention is key for dealing with rust and corrosion on brake components. Clean and inspect regularly to detect potential issues before they worsen. Follow preventive maintenance measures, such as removing rust and corrosion and applying grease or lubricant, to avoid stuck rotors.
Using a breaker bar for leverage
- Using a breaker bar for leverage can be effective when dealing with a stuck brake rotor. Position the bar’s head onto one of the lug nuts on the rotor. Make sure it fits securely, without slipping. Apply downward pressure on the end of the bar, using body weight for additional force. This helps loosen the rotor by leveraging against the resistance. Hold onto the bar with one hand while applying pressure.
- Rotate the rotor in both directions to break any rust or corrosion causing it to stick. If needed, use your other hand or get someone to help provide further leverage. Hold onto another part of the vehicle while exerting force on the bar.
- If you can’t dislodge the rotor, get professional help. Regular preventive maintenance such as cleaning rust and applying grease or lubricant to wheel hubs and rotor surfaces will reduce the likelihood of stuck rotors.
- As a last resort, use power tools like an angle grinder to cut through the rotor.
Cutting the rotor off with an angle grinder as a last resort
To start, make sure the vehicle is securely raised and supported. Wear protective gear like goggles and gloves.
Using an angle grinder with a metal-cutting blade, cut carefully near the hub. Be careful not to damage any parts or cause sparks that could set off something flammable.
Once the rotor is partially cut, use a pry bar or something similar to break it free.
Lastly, remove any bits left of the rotor and inspect for damage that needs repairing.
It’s important to remember that cutting the rotor off should be a last resort after trying other methods to avoid damaging anything and having issues. If you can’t get it off or are uncertain, ask a professional for help.
Before considering cutting the rotor off, there are other methods that can be used:
- Rotating the rotor: Try moving the rotor back and forth while pressing in both directions to loosen it.
- Penetrative lubricant: Use a lubricant designed to free rusty pieces on the area where the rotor meets the wheel hub and let it do its thing.
- Using a rotor puller: Use a tool meant for this to apply even force around the rotor while pulling it away from the hub.
- Applying heat: Heat can make metal easier to separate. Be careful when doing this and don’t heat up anything flammable.
- Using a breaker bar: Place a breaker bar or long-handled wrench on the rotor’s lug nuts and add force to try and break it free.
- Cutting the rotor off with an angle grinder as a last resort.
Be safe and controlled when trying each method, and take into account the specific situation and potential risks.
Stay prepared and prevent future stuck rotors by following preventive measures.
Preventive measures to avoid future stuck rotors
To avoid future stuck rotors, there are preventive measures you can take. Discover effective methods such as cleaning rust and corrosion, as well as applying grease or lubricant to the wheel hub and rotor surface. These practices will not only enhance your brake performance but also extend the longevity of your rotors. Keep reading to find out how to keep your rotors in optimal condition!
Cleaning rust and corrosion
Text:
Rust and corrosion can harm brake components, leading to poor performance. Cleaning rust is a critical task that can help stop further damage and increase the life of brakes. Joe, a car enthusiast, knew this and he aimed to clean off the rust from his rotor surface. Here’s what he did:
- Removed the caliper and caliper plate for better access to the rotor.
- Attached the lug nuts to the rotor so it wouldn’t move while working.
- Utilized wire brushes and sandpaper to scrub off the rust from the rotor.
- Applied penetrating oil or rust dissolver for stubborn rust.
- Put bolts into the threaded holes at the back of the rotor for leverage.
Joe’s timely attention to rust saved him from potential road accidents. He also realized that preventive maintenance measures, like regularly cleaning rust and applying grease/lubricant to wheel hubs and rotor surfaces, could help avoid stuck rotors. These steps can expand the lifespan of brake components and minimize the risk of rust and corrosion. So, don’t forget to grease up those wheels to prevent stuck rotors!
Applying grease or lubricant to the wheel hub and rotor surface
For proper grease or lube on the wheel hub and rotor surface, do this:
- Get rid of excess dirt or debris from the wheel hub and rotor surface using a brush or compressed air. This helps the lubricant stick.
- Put a thin layer of high-temp brake grease or special lube on the wheel hub using a clean cloth or brush. Make sure to cover the entire surface, particularly in areas prone to rust or corrosion.
- Then, put a small amount of grease or lube on the rotor’s mating surfaces where it meets the wheel hub. This stops binding or sticking over time.
- Last, reassemble all components in reverse order, ensuring they are properly tightened and secured.
Doing this will ensure your brake system works well and is safe from rust and corrosion. Be aware that while applying grease or lube to the wheel hub and rotor surface stops issues, it cannot fix an existing problem like a stuck rotor. In that case, you should get professional help to avoid more damage to your vehicle’s brakes.
Conclusion highlighting the importance of seeking professional help if unable to dislodge the rotor and the significance of preventive maintenance measures
Struggling to remove a brake rotor? Professional help is needed! Seek a trained professional to dislodge it properly. They have the right tools, knowledge, and experience to do the job safely. This way, you can avoid potential damage.
Preventive maintenance measures should also be taken seriously. Regular inspections, cleaning, and lubrication can identify issues before they get worse. Neglecting maintenance can result in decreased braking efficiency, longer stopping distances, and even brake failure. All of which are dangerous for your safety.
To sum it up, if you are stuck with a brake rotor, get professional help. And don’t forget to keep up with preventive maintenance. Inspect, clean, and lubricate your brakes regularly. This way, you can keep your vehicle in optimal condition and stay safe on the road.
Some Facts About How To Get Brake Rotor Off:
- ✅ Removing a stuck brake rotor can be challenging and may require specialized tools. (Source: RepairSmith)
- ✅ It is important to replace rusted components like brake pads and shoes to prevent brake failure. (Source: RepairSmith)
- ✅ To remove a stuck brake rotor, you may need to remove the brake caliper and plate and temporarily reattach the lug nuts. (Source: RepairSmith)
- ✅ Techniques like removing rust, using penetrative lubricant, applying heat, or using a breaker bar for leverage can help in removing a stuck rotor. (Source: RepairSmith)
- ✅ If all else fails, cutting the rotor off with an angle grinder is an option, but it is recommended to install a new rotor afterward. (Source: RepairSmith)
FAQs about How To Get Brake Rotor Off
How do I remove a stuck brake rotor?
Answer: To remove a stuck brake rotor, follow these steps:
- Remove the brake caliper from the bracket.
- Remove the caliper plate.
- Temporarily reattach the lug nuts.
- Remove the rust.
- Grab some extra equipment.
- Insert bolts into the threaded holes at the back of the rotor.
What are some tips to prevent a stuck rotor in the future?
Answer: Here are some tips to prevent a stuck rotor:
- Clean rusted areas and corrosion with a wire brush.
- Apply grease or lubricant to the wheel hub and rotor surface.
- Seek professional help for maintenance and inspections.
- Replace rusted components promptly to prevent brake failure.
Do I need to be a professional mechanic to remove a stuck rotor?
Answer: While it is possible to remove a stuck rotor yourself, it is recommended to let professional mechanics handle the task if you lack the technical know-how. They have the expertise and specialized tools required to safely remove the stuck rotor without causing damage to other brake components.
What should I do if the rotor is still stuck after following the steps?
Answer: If the rotor is still stuck after following the steps, you can try the following methods:
- Rotate the rotor to loosen it.
- Use a penetrating lubricant to help loosen rust.
- Use a rotor puller for extra leverage.
- Apply heat to expand the metal and break the rust seal.
- Use a breaker bar for additional leverage.
- If all else fails, cutting the rotor off with an angle grinder may be an option. However, this should only be done if you plan on installing a new rotor.
Should I seek professional assistance if I’m unable to remove the stuck rotor?
Answer: If you are unable to remove the stuck rotor or feel unsure about the process, it is best to seek professional help. Certified technicians have the knowledge, experience, and proper tools to safely and efficiently remove the stuck rotor without causing damage to other components of the brake system.
How can I safely remove a stuck brake rotor without damaging other components?
Answer: To safely remove a stuck brake rotor without damaging other components, it is important to:
- Use suitable heat and avoid excessive heat that can damage nearby parts.
- Use specialist tools like a rotor puller to avoid applying excessive force.
- Clean rusted areas and apply some grease to aid in loosening the rotor.
- Use a pry tool or metal hammer carefully to avoid causing damage.
- Take precautionary measures and seek professional assistance if needed to ensure the removal process is done safely.