Keeping your vehicle’s braking system in top shape is crucial for your safety on the road. Among the various components of this system, the brake rotor – often referred to as a brake disc – plays a vital role in the vehicle’s ability to stop. The brake pads squeeze the rotor to produce the necessary friction to halt your car. However, over time, due to this continual friction, rotors can become uneven or develop grooves, reducing their effectiveness and potentially compromising the safety of your vehicle.
Turning a brake rotor refers to the process of machining, or resurfacing, the rotor to make it smooth and even again. This procedure can be performed on a lathe, a specialized machine used for shaping metal. It’s often a more cost-effective solution compared to replacing the rotor entirely, especially when the rotor’s overall thickness is still within the manufacturer’s specifications. In the following sections, we will provide a step-by-step guide on how to turn a brake rotor, a potentially valuable skill for those interested in maintaining their vehicles.
Contents
- 1 Key Takeaways:
- 2 Types of Brake Rotors
- 3 The Process of Turning Brake Rotors
- 4 Factors Influencing the Decision to Resurface or Replace Rotors
- 5 Challenges in Turning Hat Rotors
- 6 The Decline of Brake Lathes and the Shift Towards Replacement
- 7 Importance of Proper Caliper and Pad Slide Functionality
- 8 Overall Impact of the Shift towards Replacement on the Economy
- 9 Some Facts About How To Turn a Brake Rotor:
- 10 FAQs about How To Turn A Brake Rotor
Key Takeaways:
- Turning brake rotors is a process that involves resurfacing the braking surface to improve performance and prolong the lifespan of the rotors.
- Understanding the different types of brake rotors, such as blank & smooth, drilled, slotted, and drilled & slotted rotors, can help in choosing the right type for specific driving needs.
- Signs that indicate the need for turning or replacement of brake rotors include pulsation or vibration while braking, uneven wear, and excessive noise.
- Factors influencing the decision to resurface or replace rotors include changes in brake rotor design and the cost-effectiveness of replacement.
- Turning hat rotors can pose challenges due to their lightweight nature and the potential for incorrect mounting, requiring careful attention during the turning process.
- The decline of brake lathes and the shift towards rotor replacement is driven by factors such as economic viability, the prevalence of rotors that are beyond repair, and advancements in brake technology.
- Proper caliper and pad slide functionality is crucial for maintaining optimal braking performance and preventing premature wear of brake rotors.
- The shift towards rotor replacement has had an overall impact on the economy, affecting industries such as automotive repair and manufacturing.
Types of Brake Rotors
Brake rotors are an important part of vehicles’ braking systems. Different types exist, each with its own characteristics and functions. It’s essential to know the types for the right choice when driving.
- Blank & Smooth Rotors: Smooth, with no holes or slots – these rotors provide consistent braking & are great for everyday driving & normal road conditions.
- Drilled Rotors: Holes are drilled – to dissipate heat & avoid brake fade. Plus, better water & gas evacuation. However, they may be prone to cracking under heavy stress or extreme driving conditions.
- Slotted Rotors: Slots are cut – to remove debris & expel gases during braking. This improves pad bite & reduces risk of brake fade. Slotted rotors are often used in high-performance applications or heavy-duty vehicles.
- Drilled & Slotted Rotors: Both drilling & slotting techniques here. Improved heat dissipation, gas evacuation, debris removal, & enhanced pad bite. Commonly used in performance vehicles that require superior stopping power.
- Hat Rotors (Unique Detail): Lightweight design, with a center hat section that attaches to the wheel hub. Reduces unsprung weight while maintaining structural integrity. Found in high-performance sports cars needing weight reduction for optimal handling.
It pays to know the types of brake rotors – for daily commuting or performance driving. The right rotor makes a big difference in braking performance & safety.
Blank & Smooth Rotors
Blank & Smooth Rotors are an ideal brake rotor choice. They have a plain and smooth surface – no holes, slots, or patterns. With a consistent surface, brake pads make contact evenly, ensuring smooth braking performance. No holes or slots means less brake pad material builds up, reducing the risk of brake fade and improving braking efficiency.
These rotors are great for drivers who value reliable braking. The smooth surface allows brake pads to disperse friction and heat evenly, minimizing wear and tear on rotors and brake pads. Blank & Smooth Rotors keep your braking system running smoothly, no matter the driving conditions.
Drilled Rotors
Drilled rotors, also known as perforated rotors, have holes running through their surface. These holes offer multiple advantages, including better heat dissipation and reduced risk of brake fade.
- Heat Dissipation: The drilled holes permit better airflow, helping to cool down the rotor during heavy braking.
- Brake Fade Prevention: Excessive heat generated from the friction of brake pads and rotors can lead to a loss in braking power. The drilled holes allow these hot gases to escape more easily.
- Enhanced Wet Weather Performance: The drilled holes also channel water away from the braking surface, reducing the risk of hydroplaning.
However, drilled rotors may crack under extreme stress or heavy-duty applications. So, they may not suit all vehicles or driving conditions.
Surprisingly, studies show that drilled rotors don’t benefit everyday driving. Slotted rotors provide similar results without many of the drawbacks of drilled rotors (source: ‘Understanding Brake Rotors and their Importance’).
Slotted rotors: Get a track day vibe every time you hit the brakes.
Slotted Rotors
Slotted rotors are a popular option for brake systems due to their many perks. They feature slots that increase air circulation, resulting in better heat dissipation and reduced brake fade risk.
For enhanced wet weather performance, these rotors have slots that channel water away from the surface. This prevents hydroplaning and ensures a better grip.
Slotted rotors also reduce pad glazing. The slots stop thermal material build-up on the rotor’s surface. This preserves optimal friction characteristics and reduces pad glazing.
In addition, slotted rotors provide increased pad bite. The edges of the slots grab onto the pad material, raising initial bite and improving braking responsiveness.
Furthermore, slotted rotors aid with dust management. The slots help to evacuate dust and debris from between the rotor and pad surfaces. This minimizes noise and maintains better contact between them.
Moreover, slotted rotors can contribute to extended rotor life compared to traditional smooth rotors. By regulating temperatures and preventing excessive wear, slotted rotors can increase the lifespan of the braking system.
It is important to note that slotted rotors may create slightly more noise than smooth or drilled rotors. Though, if extreme racing or heavy towing is involved, drilled rotors may be a better option as they provide additional heat dissipation capabilities.
Ultimately, the choice between slotted, smooth, or drilled rotors depends on individual preferences, driving habits, and specific application requirements. So, consider these factors and make an informed decision.
In summary, slotted rotors boast advantages like improved cooling, wet weather performance, reduced pad glazing, increased pad bite, dust management, and longer rotor life. They are a great option for optimizing brake performance.
Drilled & Slotted Rotors
Drilled and slotted rotors are two common types of brake rotors that provide improved performance and durability over traditional models.
These rotors have holes and slots strategically placed, which offer several benefits for braking systems.
Improved heat dissipation is one of them. The drilled holes help to reduce the risk of brake fade during intense braking.
This is especially vital in high-performance vehicles or applications with frequent and aggressive braking.
Slots on the surface of the rotors help evacuate water, mud, and debris from the contact area between the rotor and brake pad.
This adds consistent friction, improving braking performance in wet or harsh conditions.
The holes and slots also counter brake pad glazing, refreshing the pad’s surface and preventing the loss of stopping power.
Drilled and slotted rotors have better bite and initial response than smooth rotors, due to more edges for the brake pads to bite into.
These advantages make them a popular choice for performance and heavy-duty vehicles.
It is important to properly install, maintain, and inspect drilled and slotted rotors, to ensure optimal performance and longevity.
Following manufacturer recommendations for bedding-in new brake pads can prevent uneven wear on the rotor surface.
The Process of Turning Brake Rotors
The process of turning brake rotors involves addressing their purpose and recognizing the signs that indicate the need for turning or replacement. Understanding the significance of turning brake rotors and being aware of the warning signs can ensure the effective functioning and safety of your vehicle.
Purpose of Turning Brake Rotors
Turning brake rotors means resurfacing the braking surface of the rotor. This is done with a brake lathe to remove any imperfections or wear. It helps restore smoothness and parallelism, which boosts performance and extends the rotor’s lifespan.
Friction during braking generates heat. This can cause uneven wear and warping. Turning brake rotors helps by creating an even surface for the brake pads to make contact with. This improves braking efficiency, reduces vibration, and minimizes noise.
Turning brake rotors also allows customization. For example, if the vehicle is used for high-performance driving or towing, a mechanic may choose to turn the rotors with cross-drilled holes or slots for better heat dissipation.
Turning is often a cost-effective solution. It allows for extended use of existing rotors while maintaining adequate functionality. However, it’s important to consider design changes and cost-effectiveness before deciding whether to resurface or replace them.
Hat rotors are lightweight and require caution when mounting to vehicles. Incorrect mounting can lead to improper alignment and compromised functionality.
Signs that indicate the need for Turning or Replacement
The condition of brake rotors is essential for a vehicle’s performance and safety. Over time, these rotors may become worn, necessitating either turning or replacement. Turning refers to the process of restoring the rotor’s smoothness and flatness. When damage or wear is too extensive, replacement is needed.
There are a few signs that point to turning or replacement. Cracks or deep groove marks can decrease braking performance and cause failure. If you feel pulsation or vibration when braking, the rotors are warped. Uneven thickness across the rotor means it isn’t flat, affecting stopping power. Keep an eye out for scoring and pitting too. Scoring is lines or gouges caused by debris or the wrong brake pad material. Pitting is craters or indentations caused by corrosion, impairing braking.
Rust formation on brake rotors accelerates wear, decreases braking efficiency, and produces noise. Significant rusting might mean turning or replacement. If you notice a significant decrease in stopping power, the rotors are worn and need either turning or replacement.
Design changes and cost-effectiveness also influence the decision between resurfacing and replacing. Brake lathes are being replaced due to cost and difficulty. Proper caliper and pad slide functionality is essential for optimal brake performance. Resurfacing is becoming less common due to factors making rotors scrap.
Factors Influencing the Decision to Resurface or Replace Rotors
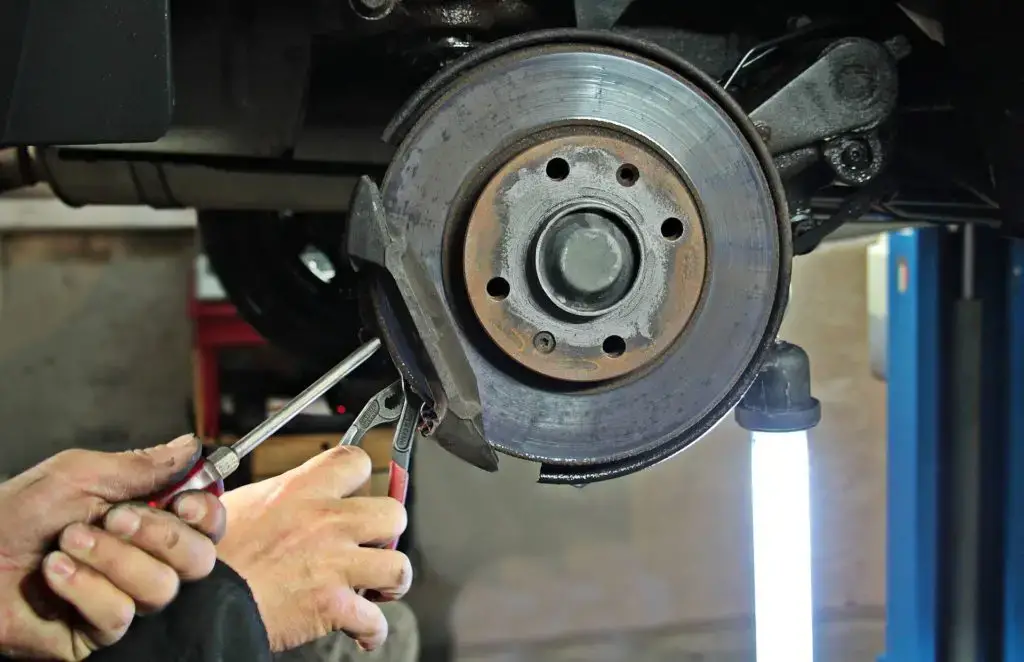
Factors influencing the decision to resurface or replace rotors – We will explore the changes in brake rotor design and the cost-effectiveness of replacement, providing valuable insights for making an informed decision.
Changes in Brake Rotor Design
Introducing blank, smooth rotors with larger contact areas for the pads – providing better stopping power and reducing brake fade. Drilled rotors have small holes to help disperse heat, while slotted rotors have grooves to evacuate gases and water. The combination of drilling and slotting is seen in drilled & slotted rotors, for maximum performance.
Manufacturers are continuously innovating brake rotor designs to ensure safety and optimal braking performance. Advances in materials science and manufacturing technologies have enabled the production of lighter, high-performance rotors with improved strength and heat resistance. Computer modeling techniques have further optimized rotor designs, meeting the demands of modern vehicles.
Save money by replacing rotors and go on a guilt-free shopping spree!
Cost-effectiveness of Replacement
Replacing brake rotors is becoming more cost-effective. Changes in rotor design complicate resurfacing. Prices for resurfacing services have risen due to fewer shops offering the service. Severe damage or wear may make replacement the only option.
Design advancements make resurfacing tougher and pricier. Brake lathe decline adds to the cost-effectiveness of replacing rotors. Resurfacing isn’t possible or practical when rotors are severely worn or damaged.
History shows market forces and tech progress drive changes in industry practices. Replacement is often the better choice for consumers and businesses.
Challenges in Turning Hat Rotors
When it comes to turning hat rotors, there are specific challenges that need to be addressed. From the lightweight nature of these rotors to the issue of incorrect mounting, these sub-sections shed light on the obstacles encountered in this process. Understanding these challenges and finding effective solutions is crucial for anyone dealing with hat rotors.
Lightweight Nature of Hat Rotors
Text:
Hat rotors are a popular choice for vehicles. They are lightweight which gives several advantages. These rotors have a center hat or bell-shaped section that connects to the hub. This lessens the weight.
The reduced weight has a good effect on the vehicle’s performance. It reduces the unsprung weight and rotational inertia. This improves acceleration, handling, and fuel efficiency.
The lightness helps with heat dissipation when brakes are used heavily. It also reduces stress on the other components in the braking system.
Hat rotors are also compatible with high-performance vehicles. The lighter weight boosts braking performance. It enables quicker deceleration and better control.
When considering brake rotors for your vehicle, keep in mind the benefits of weight reduction, heat dissipation, and compatibility. Speak to a professional mechanic for advice.
Fitting the rotor incorrectly is like trying to fit a square peg into a round hole. This can be dangerous for your brakes and you as a driver.
Incorrect Mounting Issues
Mounting issues can be tricky when dealing with hat rotors. They’re lightweight, so incorrect mounting can lead to performance problems. Mechanics have to be careful to make sure these issues don’t affect the vehicle’s braking system. It’s important to address these issues quickly.
Brake lathes are no longer the go-to for dealing with mounting issues. Mechanics must adapt to the changing automotive repair needs. They must explore alternative methods for addressing these mounting issues.
The Decline of Brake Lathes and the Shift Towards Replacement
As brake technology advances, the decline of brake lathes becomes more apparent, and a shift towards rotor replacement takes place. In this section, we’ll uncover the economic viability of resurfacing rotors and explore the factors that deem a rotor unrepairable. So, join us as we dive into the changing landscape of brake maintenance and the reasons behind the fading popularity of brake lathes.
Economic Viability of Resurfacing
Resurfacing brake rotors can be cheaper than replacing them, especially if the rotors are still in good condition. This can extend their lifespan and save money. It is especially beneficial when dealing with high-performance or specialized rotors. Resurfacing also helps improve braking performance, ensures optimal friction, and reduces noise and vibration.
Yet, resurfacing may not be economical or practical in some cases. For example, changes in rotor design may require replacement. Additionally, if resurfacing costs more than purchasing new rotors, replacement may be better. Assessing these factors is key when deciding if resurfacing or replacement is more economical. Despite this, resurfacing is still a popular choice for maintaining and prolonging brake rotor life.
Factors that render a Rotor Scrap
It’s important to understand that other factors may also cause a rotor to be scrapped. These could include improper installation or misuse, which can cause unrepairable damage. Address these issues and make sure to follow good maintenance and usage practices to prolong rotor life and avoid replacements.
When faced with a potential scrap rotor, here are some tips:
- Inspect and maintain regularly to spot early signs of wear or damage.
- Follow the manufacturer’s guidelines for usage and maintenance.
- Invest in high-quality rotors from reputable brands.
By understanding the scrapping factors and taking proactive measures, vehicle owners can save time and money while staying safe on the roads.
The decline towards replacements rather than resurfacing is due to various factors:
- Resurfacing may not be as economically viable as replacing it due to labor costs, availability of affordable replacements, and newer rotor designs that might not be suitable for resurfacing.
- Rotors with extensive wear or damage beyond the point of resurfacing would require complete replacement.
To guarantee safety and save both time and money, proper caliper and pad slide functionality is essential for smooth stops.
Importance of Proper Caliper and Pad Slide Functionality
Caliper and pad slide efficiency are critical for quality brake rotor performance. They are vital for smooth, even contact with the rotor. This allows for optimal braking power and control, which is key for safety and avoiding accidents.
Lubrication also matters. Applying lubricant to the sliding surfaces minimizes friction. This allows the caliper and pads to engage and disengage from the rotor efficiently. This leads to improved braking performance. Regular maintenance and inspection are necessary for early detection of any issues and the prevention of brake system failures.
It’s essential to prioritize caliper and pad slide functionality. It enhances the driving experience and ensures the safety of yourself and others. Don’t overlook this important maintenance task. It can make a huge difference in performance and longevity of your brake system. Be proactive and be safe!
Overall Impact of the Shift towards Replacement on the Economy
The move towards replacement in the economy has had a large overall effect. As businesses modify for new technology, there is a larger need for changing out-of-date equipment and parts. This shift has made new opportunities for companies involved in the making and giving away of replacement pieces.
One place where the shift towards replacement has had a major effect is the car industry. With progress in-car tech, the requirement for replacement parts such as brake rotors has risen. As buyers choose to replace worn-out brake rotors instead of fixing them, it has increased the growth of the replacement parts market. This shift has not only helped out manufacturers and distributors of replacement brake rotors but also given rise to new job chances in the industry.
The trend towards replacement has also had a good result on the complete economy by encouraging innovation and technological progress. As industries try to meet the demand for replacement products, they put money into research and development to enhance the quality, longevity, and effectiveness of these pieces. This, in turn, drives technical development and boosts economic growth. Moreover, more production and sale of replacement parts add to the complete economic activity by making a multiplier effect on many related industries.
To take full advantage of the openings given by the shift towards replacement, businesses need to adjust and accept this change. By staying up-to-date with the most recent tech trends and always enhancing their products, companies can place themselves as leaders in the replacement market. Not doing so may result in missing out on potential benefits and dropping competitiveness in the changing economy. It’s essential for companies to join in the replacement economy to make sure long-term success and sustainability.
Some Facts About How To Turn a Brake Rotor:
- ✅ Turning a rotor is the process of using a specialized machine to return the friction surface of the rotor to a perfectly flat state. (Source: Team Research)
- ✅ Rotor resurfacing is not as common as it used to be, as many of today’s rotors are thinner and may not be suitable for resurfacing. (Source: Team Research)
- ✅ Resurfacing rotors requires expensive equipment and a qualified mechanic, and it should never be done as a DIY job. (Source: Team Research)
- ✅ O’Reilly and Pep Boys are the only major auto parts chains that offer rotor resurfacing. (Source: Team Research)
- ✅ Factors such as scoring, cracking, corrosion, and warping can prevent rotors from being turned and may require replacement instead. (Source: Team Research)
FAQs about How To Turn A Brake Rotor
What is brake rotor resurfacing?
Brake rotor resurfacing, also known as turning, is the process of using specialized machining equipment to restore the friction surface of the rotor to a perfectly flat state.
Why is brake rotor resurfacing necessary?
As brake pads wear down, the friction surface of the rotor also wears and develops grooves and deposits. Resurfacing the rotor ensures optimal contact between the pads and rotor, maximizing braking performance.
Can all brake rotors be resurfaced?
No, not all brake rotors can be resurfaced. Many of today’s rotors are thinner and may not have enough material to be resurfaced. Factors such as scoring, cracking, corrosion, and warping can also prevent rotors from being turned.
Is brake rotor resurfacing a DIY job?
No, brake rotor resurfacing is not a DIY job. It requires expensive machining equipment and should only be done by a qualified mechanic.
How much does brake rotor resurfacing cost?
The cost of turning rotors can vary, but you can expect to pay around $200 per axle. It takes about 2 hours of labor to turn rotors, and they should never be turned more than once.
Where can I get my brake rotors resurfaced?
O’Reilly and Pep Boys are the only major auto parts chains that offer rotor resurfacing. However, not all locations may have the necessary equipment, so it’s best to call ahead and confirm. AutoZone and Advance Auto Parts, on the other hand, do not offer rotor resurfacing.